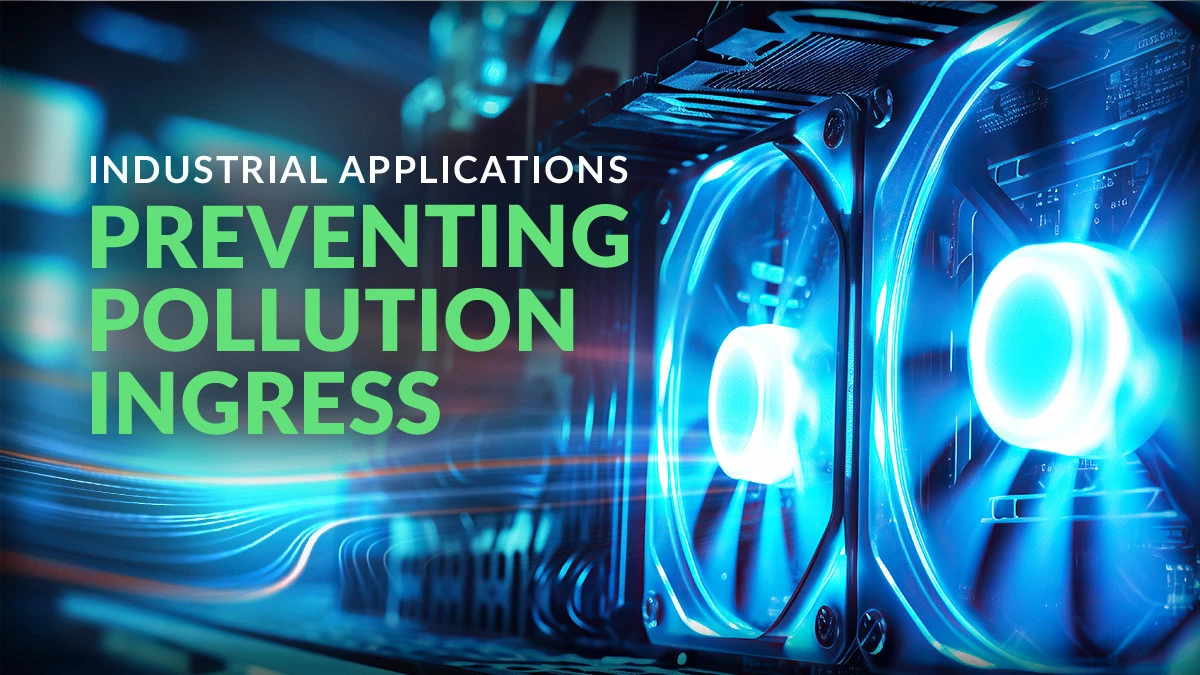
Pollution ingress not only increases operating temperatures but also reduces design margins, leading to decreased reliability and shortened device lifespans.
This blog examines the most effective strategies for mitigating pollution in a power supply while maintaining optimal functionality so that your device functions exactly as you’d expect.
Overview
- Fan cooling systems can exacerbate pollution ingress by drawing in airborne particles.
- High IP-rated enclosures are needed to prevent dust and pollutants from entering electronic equipment
- Conduction cooling is often required to dissipate heat efficiently in sealed environments.
- The best solution is conduction or convection cooled with safety and EMC approvals.
Impact on reliability and cooling solutions
Pollution ingress in electronic equipment for industrial applications or harsh environments causes increased operating temperature and reduces design margins resulting in reduced reliability and lifetime and increased maintenance costs.
The use of fan cooling exacerbates pollution ingress, acting like a vacuum cleaner collecting surrounding airborne particles and depositing them within the electronics sub-assemblies within the end equipment or collecting them in air filters which require scheduled maintenance.
The use of high IP rated enclosures to prevent dust and pollution ingress is desirable in these environments, but often requires the use of conduction cooling to remove heat from the enclosure to ensure reliable operation and ensure adequate service life.
The power solution features most effective against pollution ingress
Designers of electronic systems for industrial and harsh environments need a power solution that is high efficiency, conduction or convection cooled to minimize or eliminate pollution ingress, and incorporates the specifications and features demanded by ever increasing power demands in a variety of industrial and infrastructure settings. The power solution, or converter, should be easy to integrate with EMC and safety approvals to enable successful integration and certification for the end application.
Thermal optimization through conduction cooling design
Conduction cooled power converters are designed so that the components dissipating most of the power, such as power MOSFETs, rectifier diodes, power transformers, and PFC inductors, are thermally connected to an interface designed to conduct heat to the equipment enclosure, removing the majority of the waste heat to the outside world, minimizing the internal temperature rise and optimizing reliability and service life.A high performance power solution for fanless and IP rated applications
XP’s new CCP550 series of AC-DC power supplies with its compact size, low profile, high efficiency design, combined with convection and conduction cooling options, makes the range a great fit for fanless and high IP rated industrial electronics and harsh environment applications with power requirements from 200W to 400W.
The CCP550 has a compact 3” x 5” footprint, low 1.5” profile, high efficiency and high power density allowing it to be embedded into electronic equipment, with the minimal waste heat conducted to the enclosure and the outside world through the power supply baseplate.
The CCP550 Series
Flexible power handling through conduction or convection cooling
Using conduction cooling, the CCP550 readily supports up to 400W at 115VAC input and above and has minimal derating allowing up to 320W at AC input voltages as low as 90VAC input. Using convection cooling the product supports up to 300W at 125VAC and 240W at 90VAC. When convection or conduction cooled, the optional 5V standby supply is rated up to 1A, all at ambient temperatures as high as 50C.
Performance data ensures easy integration and compliance
The CCP550 power supply’s detailed product data sheet provides service life curves, based on the average operating temperature of key electrolytic capacitors. This specific product data can be used to predict the product service life when installed in the application based on the component temperatures, daily usage, and thermal mission profile of the equipment in its unique cooling environment.
The comprehensive data sheet also identifies maximum key component temperatures for safety compliance, ensuring that the cooling in the end application is adequate for system safety approvals.
Meeting industrial electronic global safety standards
CCP550 series power supplies have global safety agency approvals for industrial electronics and technology applications including IEC62368-1, EN62368-1 and UL62368-1. The CCP550 is also independently certified to comply with the latest EMC standards.
Successful integration and trouble-free development
XP Power’s applications engineering team are always available to advise and assist with the integration of our power solutions in an optimal manner, to confirm that end applications will achieve the desired service life through correct thermal management and to consult on appropriate installation and cabling protocols to ensure safety and EMC compliance.
Summary
Pollution ingress significantly impacts the reliability and lifespan of electronic equipment in industrial applications. This calls for high efficiency power solutions like the CCP550 series which supports flexible cooling options and meets stringent safety and EMC standards.
By employing conduction and convection cooling, the CCP550 ensures optimal performance while effectively mitigating the adverse effects of contaminants in harsh environments.
Explore the CCP550 series - Industrial safety approvals and versatile cooling options.